If you are looking for the best inventory management software for manufacturing, you’ve come to the right place. Below is our selection of the cream of the crop to help you make your choice.
Fabrico
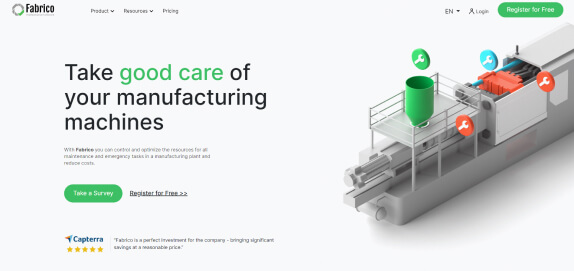
With its specialised spare parts management functionality, Fabrico stands out as a top CMMS when a manufacturing organisation requires a comprehensive maintenance management solution. It is designed to help organisations efficiently manage and supervise their maintenance activities, including spare parts management.
The inventory management feature within the software, designed for manufacturers, offers ample benefits and functionalities to help organizations effectively manage their spare parts.
Some examples of how Fabrico’s software does this include:
- Delivery and storage of spare parts and materials: When your materials and spare parts arrive, you will place them in specific locations. However, when a maintenance technician needs to access these, they will need to know where this inventory is. You can now easily manage inventory for your maintenance crews and manufacturing process by giving them the right location of the spare parts and materials. This way you ensure they don’t waste time looking for them, affording greater visibility.
- Writing off spare parts by the responsible technician: As a maintenance technician works and uses spare parts and materials for the maintenance job, they can use Fabrico’s software during a work order to accurately track inventory and cost control.
- Notifications of minimum quantity: It’s always a good idea to set minimum quantity thresholds for your spare parts. This is essential because you will never be left without a necessary part and spend days waiting for its delivery. With Fabrico, you will receive a notification when your inventory levels are low. It’s an excellent way to avoid stockouts and downtime.
- Integration with accounting software: Whatever accounting software you use, you can always rely on it to be constantly updated with changes in stock levels. In addition, you will be able to carry out inventory control and keep track of costs in one place.
Key Features
- Delivery and storage of spare parts and materials
- Writing off spare parts by the responsible technician
- Notification of minimum quantities
- Integration with accounting software
- QR code scanning and a mobile app
- Cloud-based
Price
Free trial: A free trial is available for all users who want to experience the product with full access to all features and functionalities.
- Light: Contact us for a quote
- Full: Contact us for a quote
- Enterprise: Custom pricing, which includes all the features plus an unlimited number of users and data. Other additional bonus features include a dedicated account manager, tailored features, staff training and custom SLAs.
MaintainX
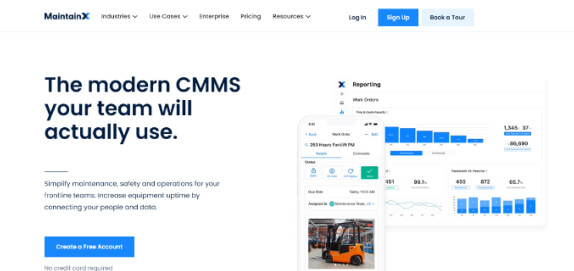
MaintainX’s parts inventory management system offers users a comprehensive package to help manage stock and spare parts seamlessly. Users can take advantage of low inventory alerts. Through this feature, they can create new purchase orders when inventory levels are low. This feature also enables maintenance teams to calculate reorder points to get inventory at the right time.
In addition to alerts, the software also provides an inventory reporting functionality. This enables smooth reporting and cost tracking of the full range of materials in your inventory arsenal. What’s great about this feature is that every user will easily be able to understand where most parts are being used. In turn, this helps crews make better decisions about forecasting costs, inventory and the required capital needed to purchase more stock.
Once a spare part or material is taken out of your inventory repository, it can be scanned with a QR or barcode scanner. This immediately tells the system that a spare part has been taken out of storage and has been put into circulation in your manufacturing plant. It’s a good way to help maintenance crews keep better track of inventory.
Finally, MaintainX offers a searchable parts history. Because every change in your inventory is recorded, it has a digital audit trail. Through this feature, users can add comments and/or images to explain to other team members why changes were made and help provide a full inventory log.
Key Features
- Low inventory alerts
- Full inventory reporting
- QR and barcode scanning
- Searchable parts history
Price
Free trial: The Basic pricing option costs $0 per user/month and it is free for lifetime usage. This package is suitable for small teams that need digitised work orders they can track.
- Essential: $21 per user/month
- Premium: $59 per user/month
- Enterprise: Custom pricing, depending on an organisation’s needs.
UpKeep
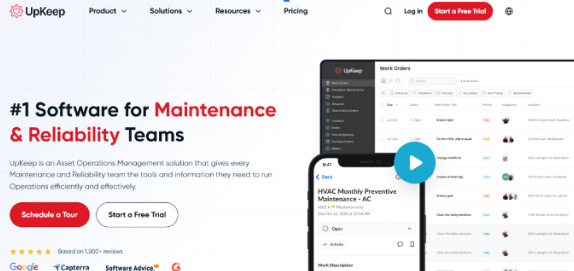
UpKeep also offers inventory management software for manufacturing, starting with barcodes to ensure consistent documentation. You can create a barcode with a single click for any part in your inventory vault. This means that maintenance technicians will be able to instantly populate work orders when they scan the spare part’s unique barcode.
Preventing downtime is another feature of this system. It works when you assign a minimum quantity value to every part. Your maintenance team will be notified once the minimum level is reached or when stock is running low.
A further perk of the feature is the insights it offers. When inventory counts are added to work orders, they are automatically updated. That allows for instant determination of the location and quantity of parts you have in stock. You can avoid overordering and spending excessively on express delivery of parts. What’s more, purchase orders can be simplified and created as PDFs with a few clicks.
If you are looking for business insights, the system offers these, too. For example, through data visualisations, you can determine what parts have cost you over time. It’s also a great way to identify any trends related to work order costs, which can help reduce unnecessary expenses.
Last but not least, maintenance crews can not only access information on the platform from any location; they can view historical records of previous diagnostic information. Through the inventory management app, streamlining operations becomes simpler and more agile.
Key Features
- Consistent documentation with barcodes
- Accurate part quantities with minimum quantity levels
- Automatically updated inventory counts
- Simplified purchase orders through notifications
- Data visualisations for business intelligence
- Parts information can be accessed from any location
- Mobile application
Price
Free trial: UpKeep’s most popular pricing package—Business Plus—can be accessed for free. Otherwise, this package comes with custom pricing that is available upon request.
- Lite: $20 per user/month
- Starter: $45 per user/month
- Professional: $75 per user/month
Fiix
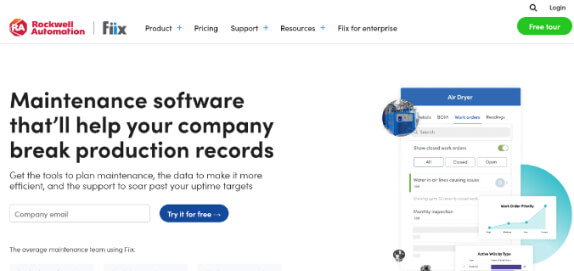
Fiix’s inventory management software for manufacturing companies enables maintenance professionals to purchase inventory with confidence.
For example, you can simplify your purchasing process by setting minimum stock quantities. In addition, the system allows users to share information between their CMMS and ERP. Furthermore, vendor information is stored and recorded in one place.
Another way in which this system helps is by aiding in organising and using inventory. You will always have confidence knowing that your inventory levels are accurate. The right spare part can be found in seconds, and these can be shared across facilities.
Tracking and reporting of spare part levels, costs and usage is also possible, helping organisations glean valuable insights and make faster, more efficient data-driven decisions. You will be able to search for parts and supply information easily while implementing the FIFO principle.
In addition, data can be viewed, sorted and explored through visualisations. The parts forecaster report tool, which is available on the analytics dashboard, helps you determine what parts to order and when. Furthermore, it informs you of the quantities needed.
Key Features
- Inventory purchasing
- Inventory organisation and use
- Inventory tracking and reporting
Price
Free trial: Fiix offers users a trial valued at $0.
- Basic: $45 per user/month. One month free with annual billing.
- Professional: $75 per user/month. One month free with annual billing.
- Enterprise: This package comes with custom pricing, which is available upon request.
IBM Maximo
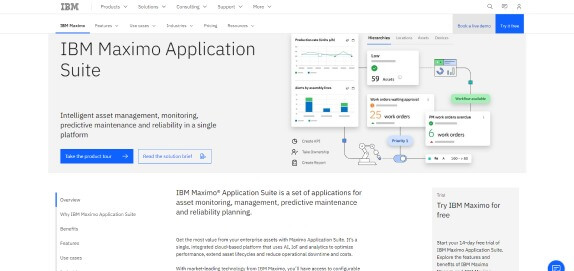
IBM Maximo’s inventory management software for manufacturing businesses helps with role-based dashboards. These are configurable and provide swift access to your organisational apps and next actions. Meanwhile, automating approvals makes repetitive tasks much simpler. Ultimately, this software can help organisations reduce downtime and costs, as well as extend asset life cycles while optimising and automating asset management.
Best-practice industry data models and workflows can help expedite operations while asset management processes are unified. Through such unification, organisations can customise workspaces, work plans and add-ons that help teams gain instant access to information about critical tasks.
Key Features
- Configurable role-based dashboards
- Industry data models and workflows
- A unified asset management process
- Financial and performance analytics
- Optimised maintenance processes
Price
- Free trial: The IBM Maximo system does not come with the option of a free trial.
- Essentials: This package comprises maintenance and inspection options.
- Standard: A quote is available upon request.
- Premium: A quote is available upon request.
- Software only: A quote is available upon request.
Limble
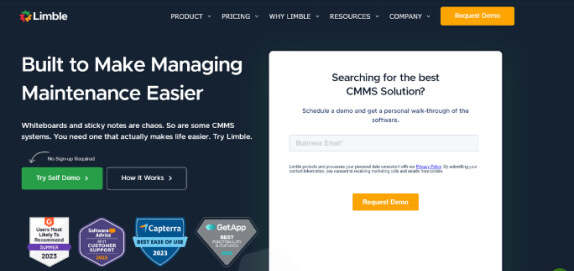
With Limble’s inventory management software for the manufacturing industry, a maintenance team can easily organise inventory and take advantage of tracking, reports and forecasting as well as custom purchasing workflows. Each of these aspects is discussed in more detail below.
When it comes to organising inventory, Limble enables teams to instantly check what spare parts are in stock, where they are located and when their quantities will be depleted. This is done through barcodes for easy lookups. In addition, maintenance teams will receive instant push and email notifications every time the inventory is updated—either when parts are low on supply or when new ones arrive. An accurate inventory status can help meet needs in real time.
With inventory tracking, reporting and forecasting, organisations can streamline their operations while maximising asset efficiency. This is done through real-time reports and automatic parts usage tracking, showing which parts were used and their costs. Forecasting is also possible as is tracking unused parts.
And lastly, the software can help organisations with inventory purchasing to prevent the build-up of unnecessary or outdated spare parts. Moreover, custom purchasing workflows mean that product orders can be automatically sent to your vendors.
Key Features
- Inventory organisation and management
- Tracking, reporting and forecasting
- Barcode lookups
- Push and email notifications
- Custom inventory purchasing workflows
Price
Free trial: The Basic pricing model is free and comes with some limited functionalities.
- Standard: $28 per user/month. A monthly subscription is $23 per user/month.
- Premium: $69 per user/month. A monthly subscription is $59 per user/month.
- Enterprise: To take advantage of this pricing plan, a custom quote is available upon request.
eMaint
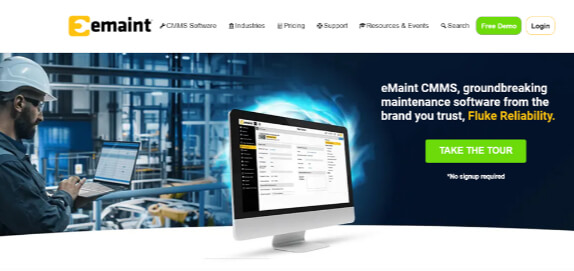
The last inventory software for small manufacturing businesses on our list is eMaint. It can help organisations save time in locating parts, reduce expedited shipping costs, streamline the parts issuing process, eliminate data entry and duplication and gain control over their inventory.
Tracking spare parts is easy, as you can navigate the platform to find what your team needs. Once you’ve done this, you can assign work orders to get the maintenance task done. When you have all the spare parts in your inventory, you will have greater confidence and control over maintenance emergencies.
Organisations will also be able to optimise inventory levels to prevent shortages and overspending. A threshold can be set for minimum stock quantities that can be replenished before it’s too late. Also, you can request and share spare parts across different facilities located at different physical locations. This manufacturing inventory software platform also enables you to view inventory reporting for the entire organisation.
Key Features
- Easy tracking and navigation of spare parts
- Assigning of spare parts to work orders
- Parts reorder list to manage inventory
- Dashboards for slow-moving parts
- Streamlined purchasing of parts
- Multi-worksite sharing of spare parts
- Mobile application for organisation-wide connectivity
Price
Free trial: eMaint offers three primary pricing plans but does not offer customers a free trial.
- Team: Pricing starts at $69 per user/month
- Professional: Pricing starts at $85 per user/month
- Enterprise: Custom quotes are available upon request.