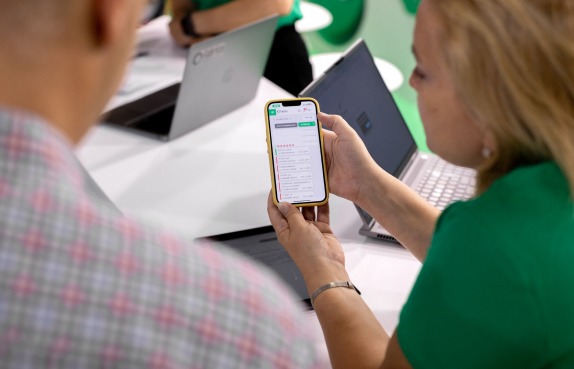
A mobile CMMS, as opposed to a traditional CMMS, enables users to perform multiple maintenance and repair tasks from their smartphones and tablets through Android or iOS applications. For example, mobile technology can engage in data entry for spare parts used, log labour hours and downtime, record failure codes, etc.
What is also possible with a mobile CMMS is to dispatch work orders in real time, collect performance data and send reports via your mobile device. Apart from these benefits, using mobile CMMS saves valuable time and resources.
Let’s explore these benefits in more detail.
Seamless remote access
Maintenance managers often oversee multiple plants at different locations. A mobile CMMS allows them to stay on track and access the system from remote locations. This enables them to issue work orders, manage maintenance technicians and repairs, monitor inventory and get detailed reports through insightful analytics at the touch of a button. Remote access makes for more seamless and efficient maintenance processes, reducing downtime and increasing organisational productivity, which is mission-critical for any maintenance department.
Quick data synchronisation
When organisations implement mobile CMMS, they can work both online and offline. Internet connectivity allows for synchronising different types of information. Working offline means data can be input into the CMMS and then synchronised and updated with the rest of the platform when it is reconnected again. Real-time connectivity facilitates harmonious data entry and data transfers and eliminates the need for duplicate processes. This way, tasks and work orders are always updated to the latest version.
QR code scanning
Inventory management is an essential element of a manufacturing facility’s maintenance operations. However, undertaking the role of managing inventory can be a constant challenge. With QR code scanning available when using mobile CMMS apps, a mobile CMMS user can easily enter significant information regarding their work process. For instance, they are able tocheck out a piece of equipment and/or the spare parts they’re taking out of the warehouse and putting into circulation on the factory floor. This means maintenance tasks are performed with efficiency, which leads to leaner inventory control, more agility, and fewer bottlenecks.
Image attachments to work orders
Work order management and repair and maintenance tasks can be made much easier for technicians and maintenance crews by sending and receiving images on their mobile devices. These images can help ensure that tasks are completed appropriately and that any challenging issues are identified in a timely manner. Giving teams visibility through image attachments can help resolve issues much faster because they’ll know the exact challenge they are facing via the visual representation.
Speedy work order distribution
A giant leap forward for maintenance and repair teams is automating work orders and moving them away from archaic, paper-based systems. With a mobile CMMS, maintenance activities such as work order distribution are done as fast as the work order is created.
Mobile maintenance management systems can help technicians carry out predictive maintenance tasks on time, every time. It leads to no delays and faster deployment times due to the ability to dispatch work orders in real time, assigned to the right technician. This provides a centralised platform that helps managers and technicians manage asset data and work orders more efficiently, reducing the risk involved in unplanned downtime.
Instant notifications
Equipment failures tend to happen at inconvenient or unplanned times. When assigning work orders, maintenance managers no longer need to worry about dispatching them to technicians manually. This is because mobile CMMS enables technicians to receive new requests for maintenance tasks to be carried out instantly with a mobile notification. This significantly speeds up the process of work order assignment, giving data in real-time. Teams can work on a repair or maintenance task as quickly as possible, increasing asset uptime and reducing operational costs and delays.
Enhanced data precision
Gone are the days of using pen and paper to record spare parts. Today, maintenance departments have the ability to track inventory, the assignment of work orders, their duration, notes left by a maintenance manager or technician, checklists and any other important information when they use a mobile CMMS. This significantly reduces the scope for data entry and maintenance schedule errors.
Additionally, when asset data is correctly entered into the system, decisions can be made quickly and more effectively in real time, ultimately benefiting your business's asset management and leading to increased productivity.