Not all maintenance is created equal. Different approaches suit different types of equipment, operational priorities, and organizational maturity.
Understanding these strategies is the first step to choosing the right mix for your facility.
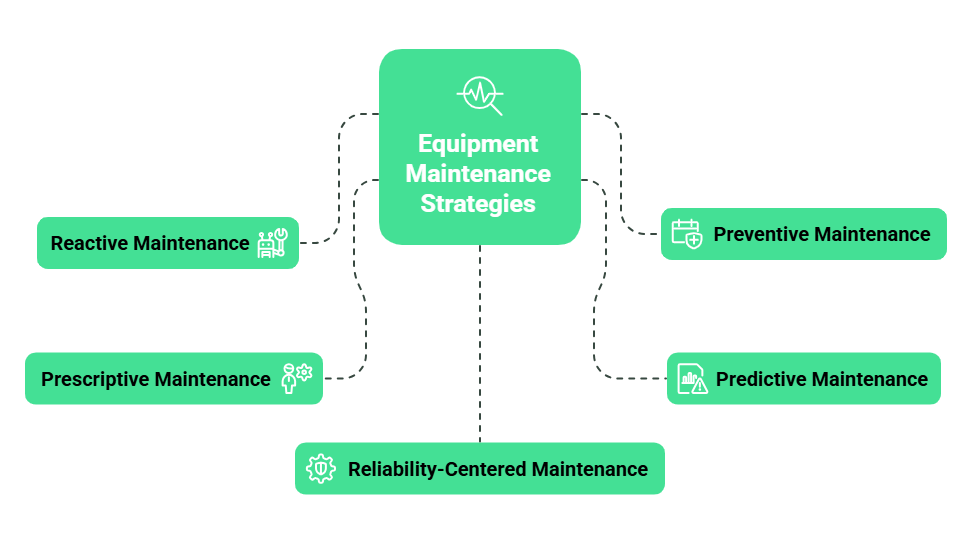
This is the most basic – and often the most problematic – form of maintenance.
- Definition: Reactive maintenance involves fixing equipment only after it has already failed or broken down. It's a purely responsive strategy.
- How it Works (or Doesn't): A machine stops working. A work order is generated (often in a panic). Technicians scramble to diagnose the problem, find parts, and make repairs, all while production is halted.
- Pros (Few and Far Between):
- Low Initial Planning: Requires minimal upfront organization or scheduling. You simply wait for something to break.
- Potentially Lower Short-Term Costs (Deceptive): If a machine rarely breaks, you might save on preventative tasks in the very short term. However, this is usually a false economy.
- Cons (Numerous and Significant):
- High Unplanned Downtime: This is the biggest killer. Breakdowns are unpredictable, leading to significant lost production, missed deadlines, and frustrated customers.
- Higher Repair Costs: Emergency repairs are almost always more expensive. Think overtime pay, expedited shipping for parts, and potentially more extensive damage because the failure wasn't caught early.
- Increased Safety Risks: Equipment running until it fails is more likely to create hazardous situations for operators.
- Potential for Cascading Failures: The failure of one component can sometimes damage other connected parts, leading to more complex and costly repairs.
- Shorter Asset Lifespan: Constantly running equipment to the point of failure puts immense stress on it, reducing its overall operational life.
- Difficult to Budget: Costs are unpredictable and can wreak havoc on your maintenance budget.
- When It's used
- For non-critical assets that have minimal impact on production if they fail.
- For equipment that is inexpensive and easily replaceable (e.g., a small office printer).
- When the cost of preventive actions genuinely outweighs the cost and impact of a failure (rare for significant industrial equipment).
For most businesses, relying solely on reactive maintenance is a recipe for inefficiency, high costs, and constant firefighting.
It's a strategy to move away from, not towards.
Preventive Maintenance (often abbreviated as PM) is a proactive strategy that involves performing regular, scheduled maintenance tasks on equipment to lessen the likelihood of it failing. It’s about taking action before a breakdown occurs.
- Definition: PM is time-based or usage-based maintenance. This means tasks are scheduled according to a predetermined calendar (e.g., monthly, quarterly) or after a certain amount of usage (e.g., every 1,000 operating hours, every 5,000 cycles).
- How it Works:
- Identify Critical Equipment: Determine which assets would most benefit from PM.
- Develop PM Task Lists: For each piece of equipment, create a list of specific maintenance tasks (e.g., inspect, clean, lubricate, replace wear parts, calibrate). These are often based on manufacturer recommendations, historical data, or industry best practices.
- Establish Frequencies: Decide how often each task needs to be performed.
- Schedule and Execute: Integrate these tasks into a maintenance schedule. Technicians then carry out the PM work as planned.
- Record Keeping: Document all PM activities, including dates, tasks performed, parts used, and any observations.
- Pros:
- Reduced Equipment Failures & Downtime: This is the primary goal and a significant advantage. By addressing potential issues proactively, you catch many problems before they cause unexpected shutdowns.
- Extended Asset Lifespan: Regular care helps equipment last longer, maximizing your return on investment.
- Improved Equipment Reliability & Efficiency: Well-maintained machines run more smoothly and closer to their optimal performance levels.
- Better Resource Planning: Maintenance work can be scheduled during planned downtimes or off-peak hours, minimizing disruption. You can also plan for necessary spare parts and labor.
- Enhanced Safety: Regular checks help identify and mitigate potential safety hazards.
- More Predictable Maintenance Costs: While there's an upfront investment in PM activities, overall maintenance costs often decrease due to fewer expensive emergency repairs.
- Cons:
- Potential for Over-Maintenance: If PM schedules are not optimized, you might perform maintenance more frequently than necessary, leading to wasted labor, parts, and even potential introduction of errors (e.g., if a perfectly good part is replaced prematurely).
- Potential for Under-Maintenance: Conversely, if schedules are too infrequent or tasks are not comprehensive enough, failures can still occur.
- Does Not Eliminate All Failures: PM reduces the likelihood of failures but doesn't guarantee they will never happen. Some failures are random and not predictable by time or usage alone.
- Requires Upfront Planning and Discipline: Setting up and adhering to a PM program takes effort, organization, and commitment.
- Examples of PM Tasks:
- Regular inspections of belts, hoses, and seals.
- Lubrication of bearings and moving parts.
- Changing filters (oil, air, hydraulic).
- Cleaning components.
- Tightening bolts and electrical connections.
- Calibrating instruments.
- Replacing parts known to wear out after a certain period (e.g., O-rings, certain types of sensors).
Preventive Maintenance is a foundational pillar of any effective maintenance program.
It represents a significant step up from purely reactive approaches.
Predictive Maintenance takes proactive care a step further. Instead of relying solely on predetermined schedules, PdM uses condition-monitoring tools and data analysis to predict when a piece of equipment is likely to fail, so maintenance can be performed just in time.
- Definition: PdM is a condition-based maintenance strategy. It involves continuously or periodically monitoring the actual condition of equipment during operation to detect early signs of degradation or potential failure.
- How it Works:
- Identify Critical Assets & Failure Modes: Determine which equipment warrants PdM and what types of failures are common or costly.
- Select Monitoring Techniques & Install Sensors: Choose appropriate condition-monitoring technologies (e.g., vibration sensors, thermal cameras, oil analysis kits, acoustic sensors) and install them on the equipment.
- Collect & Analyze Data: The sensors gather real-time or periodic data on parameters like vibration levels, temperature, oil quality, noise patterns, or electrical current. This data is then analyzed, often using specialized software or algorithms, to identify trends, anomalies, or patterns that indicate a developing fault.
- Predict Failure & Schedule Maintenance: When the analysis suggests a high probability of failure within a certain timeframe, maintenance is scheduled to address the specific issue before it leads to a breakdown.
- Refine & Optimize: Continuously review the effectiveness of the PdM program and adjust monitoring parameters, alarm thresholds, and analytical models as needed.
- Pros:
- Optimized Maintenance Schedules: Maintenance is only performed when truly necessary, minimizing unnecessary work and reducing the risks associated with over-maintenance. This means "just-in-time" repairs.
- Maximized Uptime: By catching issues at their very earliest stages, PdM can significantly reduce unplanned downtime, often more effectively than PM alone.
- Reduced Maintenance Costs: While there's an investment in monitoring technology and analytical capabilities, PdM can lead to lower overall maintenance costs by avoiding catastrophic failures, minimizing parts usage (only replacing what's needed), and optimizing labor.
- Extended Asset Lifespan: Addressing issues before they cause significant damage helps equipment last longer.
- Improved Safety: Detecting potentially hazardous conditions early enhances workplace safety.
- Increased Operational Efficiency: Equipment runs closer to peak performance for longer periods.
- Cons:
- Higher Initial Investment: Requires investment in sensors, monitoring equipment, software, and potentially specialized training for personnel to interpret the data.
- Requires Expertise: Analyzing condition-monitoring data and making accurate predictions can require specific skills and knowledge.
- Not Suitable for All Equipment: The cost and complexity of PdM may not be justifiable for all assets. It's typically applied to critical or high-value equipment where the cost of failure is very high.
- Data Overload Potential: Without proper systems and focus, you can get overwhelmed by the sheer volume of data generated.
- Examples of PdM Techniques & Technologies:
- Vibration Analysis: Detects imbalances, misalignments, bearing wear, and looseness in rotating machinery.
- Infrared Thermography (Thermal Imaging): Identifies overheating components in electrical systems, motors, and mechanical equipment.
- Oil Analysis: Assesses the condition of lubricating oils to detect wear particles, contamination, or oil degradation, indicating internal component wear.
- Acoustic Monitoring (Ultrasonic Analysis): Detects high-frequency sounds associated with leaks (air, gas, steam), electrical arcing, or early-stage bearing faults.
- Motor Current Signature Analysis (MCSA): Analyzes the electrical current drawn by motors to detect rotor bar issues, eccentricity, and other electrical or mechanical faults.
Predictive Maintenance represents a more sophisticated and data-driven approach, offering significant benefits for organizations ready to invest in the necessary technology and skills.
Prescriptive Maintenance (RxM): The Future is Now – Recommending Solutions
If Predictive Maintenance (PdM) tells you when something might fail, Prescriptive Maintenance (RxM) goes a step further: it not only predicts potential failures but also recommends specific actions to mitigate or prevent them, and can even suggest how to optimize operations based on these insights.
- Definition: RxM leverages advanced analytics, artificial intelligence (AI), and machine learning (ML) to analyze data from various sources (including PdM systems, operational data, maintenance histories, and even external factors like weather or supply chain information). It then provides actionable recommendations or, in some cases, can even trigger automated responses.
- How it Works:
- Builds on PdM: RxM typically uses the data and predictions generated by PdM as a starting point.
- Integrates Multiple Data Streams: It combines condition-monitoring data with other relevant information to get a more holistic view.
- Utilizes AI/ML Algorithms: Sophisticated algorithms analyze complex patterns and interdependencies to not just predict an outcome (like failure) but also to understand the "why" and "what to do about it."
- Generates Actionable Recommendations: The system might suggest specific repair procedures, recommend adjusting operating parameters, advise on optimal timing for maintenance considering production schedules, or even identify alternative operational strategies if a key asset is at risk.
- Potential for Automated Actions: In some advanced implementations, RxM systems can automatically adjust machine settings, order necessary spare parts, or schedule work orders.
- Pros:
- Highly Optimized Decision-Making: Provides data-driven, intelligent recommendations, moving beyond simple alerts to offer clear guidance.
- Maximizes Operational Efficiency & Uptime: By not just predicting but also prescribing solutions, RxM helps to fine-tune operations and maintenance for peak performance.
- Reduced Risk of Human Error in Diagnosis: AI can often identify complex failure patterns that might be missed by human analysis alone.
- Proactive Resource Allocation: Helps ensure the right resources (parts, labor, tools) are available and deployed optimally.
- Continuous Learning and Improvement: AI/ML models can learn from past events and outcomes, continuously refining their predictions and recommendations.
- Cons:
- Highest Complexity and Initial Investment: Requires significant investment in advanced software, powerful computing infrastructure, data integration capabilities, and specialized AI/ML expertise.
- Data Quality and Quantity are Crucial: The effectiveness of RxM is heavily dependent on the availability of large volumes of high-quality, well-structured data.
- Requires a Mature Data Infrastructure: Organizations need robust systems for data collection, storage, and processing.
- Still an Evolving Field: While incredibly promising, RxM is still a relatively new and developing area for many industries. Implementation can be challenging.
- Conceptual Example: A PdM system flags increasing vibration in a critical pump. An RxM system analyzes this, considers the current production schedule, the availability of spare parts, the historical failure modes of similar pumps, and the skills of available technicians.
It then recommends: "Schedule a replacement of bearing X within the next 48 hours. Order part Y immediately. Assign technician Z due to specialized experience. Consider reducing pump speed by 10% until repair to extend operational window if immediate shutdown is not possible."
Prescriptive Maintenance is at the cutting edge, representing the convergence of maintenance strategy with AI to create truly intelligent asset management.
Reliability-Centered Maintenance (RCM) is less a specific type of maintenance task (like PM or PdM) and more a comprehensive strategic methodology used to determine the most appropriate maintenance requirements for any physical asset in its specific operating context.
- Definition: RCM is a corporate-level, systematic approach focused on preserving the functions of equipment and systems, rather than just preserving the equipment itself. It aims to identify the most effective and efficient maintenance strategy for each asset based on its criticality, failure modes, and the consequences of those failures.
- Core Principles & Process (Simplified): RCM analysis typically involves answering seven key questions about an asset or system:
- Function: What are the intended functions and desired performance standards of the asset in its present operating context?
- Functional Failures: In what ways can it fail to fulfill its functions?
- Failure Modes: What causes each functional failure? (The specific physical reasons for failure)
- Failure Effects: What happens when each failure occurs? (The impact on operations, safety, environment, etc.)
- Failure Consequences: In what way does each failure matter? (Evaluating the severity and risk)
- Proactive Tasks: What systematic task can be performed proactively to prevent or diminish to a satisfactory degree the consequences of the failure? (This is where PM, PdM, or other actions are considered).
- Default Actions: What must be done if a suitable proactive task cannot be found? (This might include redesign, run-to-failure if consequences are low, or other default strategies).
- Pros:
- Highly Optimized Maintenance Programs: Ensures that maintenance efforts are focused where they deliver the most value, avoiding under-maintenance of critical assets and over-maintenance of less critical ones.
- Improved Safety and Environmental Integrity: Explicitly considers the consequences of failure in these areas.
- Enhanced Cost-Effectiveness: By selecting the most appropriate maintenance tasks, RCM helps achieve reliability goals at the lowest overall cost.
- Better Understanding of Assets: The rigorous analysis process provides deep insights into how equipment works, how it fails, and the impact of those failures.
- Documented and Defensible Maintenance Strategies: Provides a clear rationale for maintenance decisions.
- Cons:
- Time-Consuming and Resource-Intensive: A full RCM analysis can be a significant undertaking, requiring a dedicated team with diverse expertise (operations, maintenance, engineering).
- Requires Specialized Knowledge and Training: Proper application of RCM methodology needs skilled facilitators and participants.
- Can Be Complex: For large, intricate systems, the analysis can become very detailed.
- When RCM is Most Valuable:
- For highly critical assets where failures have severe safety, environmental, or operational consequences.
- When developing maintenance programs for new, complex equipment.
- When existing maintenance programs are perceived as ineffective or too costly.
RCM provides the overarching logic to decide which of the previously discussed maintenance types (reactive, preventive, predictive) is most appropriate for a given piece of equipment and its failure modes.
Take a live tour with a product expert