Some of the top CMMS best practices you can apply at your organisation before, during, and after implementation include the following:
1. Foster engagement across the entire organisation
Choosing a CMMS maintenance software for your plants and facilities should start with an understanding of the big picture by everyone in the organisation. This means that you should start from the top of the organisational hierarchy all the way down.
For top-level management and executives, you need to convince them of the efficiencies that a CMMS will bring. This will also have obvious cost and expense reductions and improve the return on investment (ROI).
However, if you don’t get management’s support and buy-in, you’re not likely to get very far with your CMMS implementation efforts. Middle management also needs to be convinced of the effectiveness of a CMMS solution because they will be the ones relying on it the most.
In addition, you should also involve the members of your team like technicians and engineers (including those at the junior level such as data-entry clerks). They should all know how and when to use the CMMS software to its full potential for the overall benefits of the organisation.
To achieve organisation-wide buy-in, be sure to conduct a needs assessment, create a “game plan” (including costs, time frames, savings and ROI), evaluate your current processes, identify any obstacles or bottlenecks. Be sure to set out why a CMMS is good for achieving the organisation’s goals.
2. Tailor the system to fit your specific needs
After gaining organisation-wide support for your CMMS, you need to ensure that it fits your needs. In some cases, CMMS systems may offer a lot of perks, but they may not be intuitive to use.
As such, the new CMMS must be customisable and configurable. This means different team members with different levels of skills can use it effectively and carry out better maintenance work.
When it comes to reporting and supplier management functions, access functions must be enabled for the employees who need to use them while they are disabled for others.
Other areas you should look out for include changeable elements, such as windows or labels. Alternatively, you may also wish to set up role-based user types for better separation of duties and the reduction of complexities.
The easier it is for your team to utilise the CMMS, the higher the rates of adoption and the faster the implementation process, so your organisation can then enjoy its benefits.
3. Harness the power of mobile features
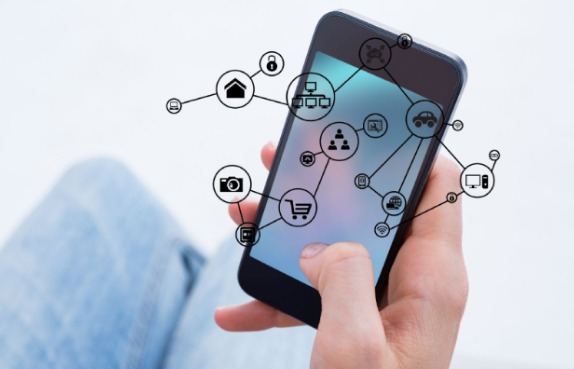
Whether you run one manufacturing plant or have several facilities, you know very well that lags in communication can be a significant drawback. With a correctly implemented CMMS, your team’s communication will improve.
This is especially enhanced when a CMMS has mobile features.
Taking advantage of the fact that almost everyone carries a mobile phone with them, they will be able to access the system from anywhere and at any time.
This can reduce costs and time spent traveling between the office and the job site. It can also make teams more effective, eliminate reliance on paper-based records and provide real-time updates and notifications.
Furthermore, a CMMS’s mobile app functionality can equip your team to take photos and videos of any mechanical problems, therefore facilitating faster and more accurate repairs. Other advantages include QR code scanning abilities, wearables integration, and smart mobile alerts.
In addition, maintenance managers can approve maintenance requests, supervise tasks and track progress in real time from any location. Ultimately, this can lead to increased productivity and efficiency.
Discover more about the benefits of a mobile CMMS, and how it can contribute to better workflow.
4. Cultivate long-term partnerships with vendors
Implementing a CMMS maintenance program takes time and careful planning.
For this purpose, your CMMS vendor should not be a fly-by-night operation. They should offer you extensive support for the duration of your licensing agreement to use their software. Customer support is crucial in all phases of CMMS implementation so that you and your team can use the new technology successfully.
Apart from customer support, you also need to have a point of contact that you can communicate with. Open channels of email and phone communication with fast response rates are a great way to clarify any issues and address potential bottlenecks.
It’s also a good way to get answers to any questions you may have, including best-use tricks that can help save time and effort. You should also inquire about software updates, how frequently they happen and what you should expect in these cases (e.g., if they are paid and how long they take).
Some CMMS providers like Fabrico offer one-day integration with easy onboarding. Although selecting the right CMMS solution should take time and testing, implementation can be made easy with the right partner that offers great levels of support and future-proofs your operations.
5. Establish an ongoing training programme
To empower your employees to use the CMMS successfully, you need to implement a training programme that helps them adapt to changes better.
Your training programme should be aimed at everyone involved in the process; from the most junior role to the most senior, such as maintenance technicians, supervisors and administrators. Training should go over system navigation, data entry, work order management, preventive maintenance scheduling, reporting and every other function your plant uses, including custom criteria.
When your team understands the capabilities and functionalities of the CMMS, they will be better equipped to use it optimally. This will result in reduced downtime, greater efficiency, streamlined processes, increased productivity and better asset reliability.
As such, your training programme should be comprehensive and include regular communication sessions, in-person workshops, video and online tutorials as well as documented materials to cater to as many different learning styles as possible.
Also worth noting is that training should be an ongoing process. This means that it should not be a once-off event only during the implementation phase but also when software updates become available.
6. Extract valuable insights through reporting
It is essential that you use your CMMS to its full potential. This means not only using it to schedule and initiate work orders and preventive maintenance tasks but also for CMMS reporting and analytics.
The right CMMS software will be able to provide you with information on your assets, such as their performance and your preventive maintenance procedures. These insights will go a long way towards helping you plan your budget and predict future requirements. In addition, insights into machinery performance and asset health can produce easily digestible data and reports through graphs and charts.
For example, you can monitor your CMMS key performance indicators (KPIs), identify patterns and gaps and evaluate how effective your strategies are. Additionally, this data can be shared with relevant people in your organisation and you can use it for enhanced decision-making.
7. Ensure service provider compliance
Most, if not all, manufacturing plants and facilities and their employees must adhere to local standards, regulations and laws. For this purpose, your CMMS provider must be properly accredited by following ISO and IFA compliance standards.
This means that your vendor must be able to assure you of full compliance with the relevant laws. As such, they will need to prove that they have the right insurance, credentials, licences and documentation. So, when an inspector arrives or an audit is due, you can have full assurance that you are covered in the event that something unanticipated happens.
Further to this, compliance management capabilities can be integrated into your maintenance programme. This means that non-accredited personnel will have limited access to the CMMS, while the accredited personnel will have fuller access.
Through this CMMS best practice, organisations can protect themselves from potential operational, financial and legal challenges.
8. Ensure the maintenance team is on board with your CMMS choice
As the main users of your CMMS platform, your maintenance team members should use and benefit from the software the most. They are considered the daily users of the platform in your organisation and will require some onboarding and training to get used to the implementation.
This aim can be achieved when your maintenance team actively uses the CMMS from the start to schedule tasks, create tasks with detailed checklists, schedule preventive maintenance tasks, keep track of spare parts and generate detailed visualisations.
The smoother flow of communication through these actions and the initiation of discussions provides more space for clarifying any issues and less room for errors being made in the future as the whole team is comfortable with the CMMS platform.
9. Implement standardised data entry criteria
A CMMS cannot function without data. When an organisation implements a CMMS, data is a crucial component of the system’s efficient functioning.
To begin the process of transferring data from a legacy system, you need to ensure you have all the relevant data in place and that it is standardised.
Data can be “cleansed” by removing duplicates, correcting errors, validating data integrity and exporting it in compatible formats. Meanwhile, standardisation can take place when there are clear guidelines for each piece of machinery’s codes, names, attributes, their part of the asset hierarchy, etc. Your team must be thoroughly trained on the entry and use of standardised data so that confusion can be avoided and potential time lost in searching for data minimised.
Once data has been cleansed and standardised, it’s time to map it to the corresponding fields in the CMMS. Luckily, some CMMS providers offer an intuitive data import function to ensure this action isn’t a hassle.
The entire process of transferring data must be completely secure and private. For this purpose, it may be necessary to perform data encryption, limit access controls and ensure compliance with data protection rules.
10. Actively measure the improvements resulting from implementing your CMMS
As the final CMMS best practice, it’s essential for you and your team to measure all the improvements resulting from the implementation of your CMMS solution.
This means measuring metrics such as improvements in productivity, reductions in downtime, reduced costs in purchasing and managing spare parts, greater team efficiency and increased asset lifespans.
When you're able to quantitatively determine the outcomes and benefits of implementing a CMMS platform in your operations, you will have a stronger foundation for future decision-making.
Furthermore, you will be able to demonstrate to board members and management all the advantages and cost savings associated with the CMMS, ultimately boosting the returns on their investment.