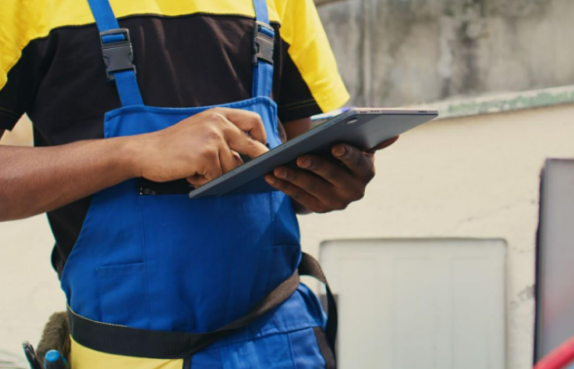
Having a preventive maintenance plan is important for many reasons. However, creating and implementing a preventive maintenance plan requires patience, foresight and prior planning.
By following the right steps in terms of how preventive maintenance plans are prepared, you can give your organisation a head start and reduce unnecessary costs and downtime, which can lead to organisational inefficiencies.
With this in mind, below we present six simple steps to creating your preventive maintenance plan.
1. Set priority goals
Every organisation has its own priorities and goals when it comes to repairs and maintenance. However, you should seriously think about these in depth so that you can clearly identify your organisational goals.
Whether it’s to boost productivity through fewer machine failures and breakdowns, catch irregularities before they occur or become a problem or ensure that your team is properly distributed across multiple repair and maintenance tasks, you need to identify your goals and then prioritise them.
Prioritising will depend on your specific organisational requirements. For some, it may be important to ensure that all machines are well-lubricated. For others, priorities may include ensuring that machines are maintained in terms of original equipment manufacturer guidelines and warranties.
Whatever your goals are, make sure they are prioritised in order of importance. This means placing those repair and maintenance needs that could lead to the largest organisational disruptions first and then working your way down the list to smaller priorities, such as changing light bulbs, etc.
2. Use preventive maintenance software
Step two, after you have set your priority goals, is to use preventive maintenance software. Often, this is referred to as a computerised maintenance management system (CMMS). What this system does is link up to all your machines and help you identify where emergency repairs or regular repairs and maintenance need to be carried out.
Furthermore, this software can help you manage your inventory alongside work orders that you assign to technicians, and it can also be a big boost for productivity because every team member will know exactly what to work on at a given time.
This is often boosted by the fact that CMMS software issues notifications to smart devices, such as smartwatches or smartphones, meaning that teams will get notified in real time about what task is a priority at the given moment.
Also, when issuing work orders for your technicians or maintenance crews, you can attach vital information and documents, such as graphs, tables, warranties, manufacturer maintenance instructions, best practices, and other aspects, to ensure that they are fully prepared for the maintenance job at hand.
3. Develop a maintenance schedule
In our brief definition of planned preventive maintenance above, we mentioned that preventive maintenance is carried out periodically. This could mean that maintenance tasks are carried out daily, weekly, fortnightly, monthly, quarterly, bi-annually or even annually. The latter is referred to as an annual preventive maintenance plan.
Naturally, the time for inspections and maintenance will vary depending on the specific asset in question. What organisations often do is implement trigger-based events to signal when maintenance needs to be carried out.
For instance, you know that your car needs to be serviced either after reaching a certain mileage or after a certain distance has been driven. The same is true for your machines and equipment. Each one has its own lifespan and warranty, and as such, each one needs to be maintained at different intervals.
CMMS software is perfect for keeping track of these maintenance tasks because when they receive a trigger, they will notify the maintenance manager of the event in question, enabling them to take timely action to maintain the asset before it breaks down.
4. Provide implementation training
As a maintenance manager who is responsible for preventive maintenance planning, there will be a lot of information and data that you will be confronted with. From priority goals to using a CMMS system, this can become a daunting task.
However, if you find this task challenging, you should not assume that your team will not feel that way either. This is why it is essential to ensure that your maintenance crew is well-trained to implement preventative maintenance tasks according to priorities, goals and clear instructions.
They need to be connected to your CMMS software and know how to receive and update work orders. They also need to have best practices in mind when carrying out a maintenance task so that your organisation can enjoy the benefits of equipment that runs like a well-oiled operation.
5. Create a preventive maintenance checklist
To cross your “t’s” and dot your “i’s”, you should also create a preventive maintenance checklist. This means that every technician operating on a given task has a checklist of items to check off the list once they start working on a task and as they finish working on it, too. This checklist is a way of double-checking that nothing has been left unattended or unaccounted for and that there are no gaps in the work carried out.
Your checklist will help you track key performance indicators (KPIs), such as mean time to repair, planned maintenance percentage and mean time between failures. What you should also do as a best practice is compare these metrics to your predetermined priority goals that you established at the outset of the process.
6. Monitor and make adjustments
Whether you use a preventive maintenance plan template or you create your own custom plan, it’s essential to remember that your work is never finished.
You will be in a continuous feedback loop through which you monitor your progress, use data to drive improvements and decisions as well as make adjustments and tweaks where necessary based on maintenance history metrics.
This will ensure that your manufacturing facility’s preventive maintenance operations are smooth and optimised for the benefit of the entire organisation.
This process, when your team performs maintenance and carries out preventive maintenance work, will involve constant fine-tuning and the involvement of all stakeholders because both your technicians and upper management need to be aware of any changes taking place so that they can react accordingly.