As a comprehensive and sophisticated platform, a CMMS must have several core features, among which are the following:
Work Order Management
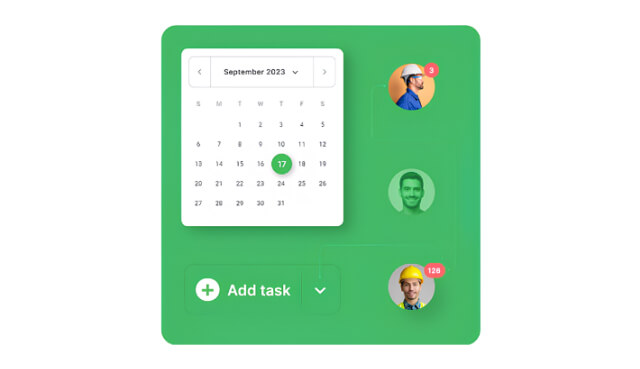
Work order management revolves around the management of work requests for maintenance or repair tasks.
It starts with the manual creation of a new work order by the relevant personnel. Usually, that's the maintenance manager. They could also automate this step, depending on specific triggers and system settings.
The maintenance work order is assigned to the responsible person (e.g. the technician) with a time frame for the task’s completion. When the specialist receives the work order, they will also receive a series of details to make their job easier. It’s also possible to attach images to the relevant task for greater levels of clarity.
One of the most convenient aspects of work scheduling is the ability to integrate it with calendar systems so that the person assigned can receive task notifications, reminders and updates straight on a mobile device and/or email.
Once the job is completed, work orders are marked as closed or completed.
Work order management comes with significant benefits for everyone on the team, helping them to:
- Streamline, structure and coordinate the entire workflow.
- Plan, prioritize and execute maintenance tasks efficiently.
- Improve communication between all stakeholders.
- Ensure proper documentation.
- Reduce response times, therefore increasing productivity.
- Promote transparency and accountability.
- Keep a record of maintenance costs for further analysis.
- Track asset performance over time.
- Gain valuable information from the work order history.
Preventive Maintenance
Prevention is at the heart of maintenance because it catches potential issues before they arise. This process is typically automated and can be scheduled based on time, meter or measurement/condition-based triggers. However, it is also possible to initiate preventative maintenance based on asset usage, manufacturer guidelines, industry standards or regulatory requirements.
Automated scheduling is a key functionality of preventative maintenance. In the task description, you can add safety protocols, spare parts, guidelines and best practices, recommended procedures, tools, etc. Following specialized checklists can streamline the maintenance process and minimize potential oversights.
The benefits of preventive maintenance are many and they include:
- Reduced equipment downtime
- Organized assets across multiple orders
- Unplanned breakdowns reduction
- Extended machine lifespans
- Maximized equipment reliability
- Reduced disruption of regular operations
Spare Parts and Inventory Management
A CMMS can handle an organization’s materials and spare part management processes, which is especially useful for inventory control and optimization.
As part of the centralized inventory, you can create a list of all spare parts stocks. This record contains valuable information, including the part’s model, quantity and location.
Additionally, the costs of restocking inventory will be immediately available and visible to the relevant person. This way, automatic resupply can take place in a timely manner without costing the organization unnecessary downtime.
It also enables decision-makers to decide on retiring or upgrading a piece of machinery when the time comes.
Reporting and Analysis
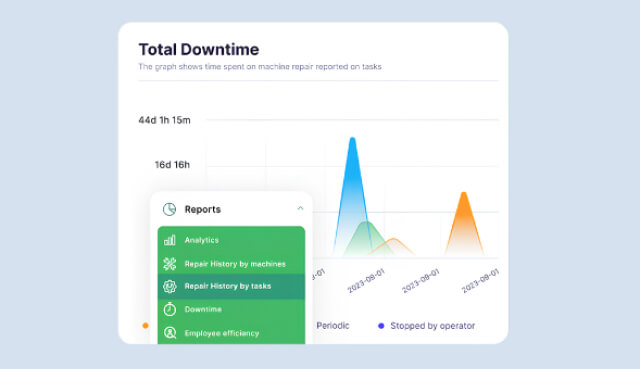
CMMS’s functionalities extend even further to providing detailed reports, giving rise to insights to base future decisions on. By enabling users to track key metrics and analyze CMMS trends, decision-makers become much more adept at recognizing areas for improvement, cost savings, and efficiencies. This, in turn, leads to more effective resource allocation and higher productivity.
This functionality also enables organizations to better measure how effective their maintenance strategies are. They can also track performance against key performance indicators (KPIs) and, as such, drive efforts toward continuous organizational growth.
Based on customizable reports and dashboards, organizations can select the area of focus at any given moment to identify patterns, enabling a proactive approach. These reports can be produced and show data in real time through accurate visualizations. In this article on CMMS report examples you can review them in detail.
Compliance and Safety Management
Because safety management is a critical aspect of organizations’ responsibility, aspects such as safety protocols and compliance standards (e.g. ISO and ITF) must be taken into account to keep staff safe and ensure conformity with regulatory organs.
With a CMMS at your side, you will be able to generate compliance reports that capture aspects such as adherence to safety and regulatory requirements. These reports can create an important audit trail that helps to ensure accountability and even identify areas that need improvement.
Labor and Resource Management
Through a CMMS, organizations can manage their labor resources. For example, it is possible to track which staff members are available to carry out the maintenance task and assign them work orders.
However, a CMMS goes beyond this as it can also organize and monitor shifts. Furthermore, employees can create time logs for more accurate labor tracking.
Mobile App
Having access to the CMMS platform on a mobile phone or tablet means that maintenance teams can manage tasks on the go conveniently and easily. With real-time updates, paperwork is eliminated while collaboration is optimized.
Through mobile devices, it’s also possible to upload and attach images, documents, and files that are related to the assigned work order.
In addition, with mobile CMMS apps, you can scan barcodes or QR codes to enable easier and quicker identification of assets, spare parts and other relevant information. It allows for better tracking of inventory as a spare part is removed from storage and put into operation.
Mobile apps can often include offline functionality in areas without access to the internet. This means that work is never halted and can continue in the most efficient manner possible.