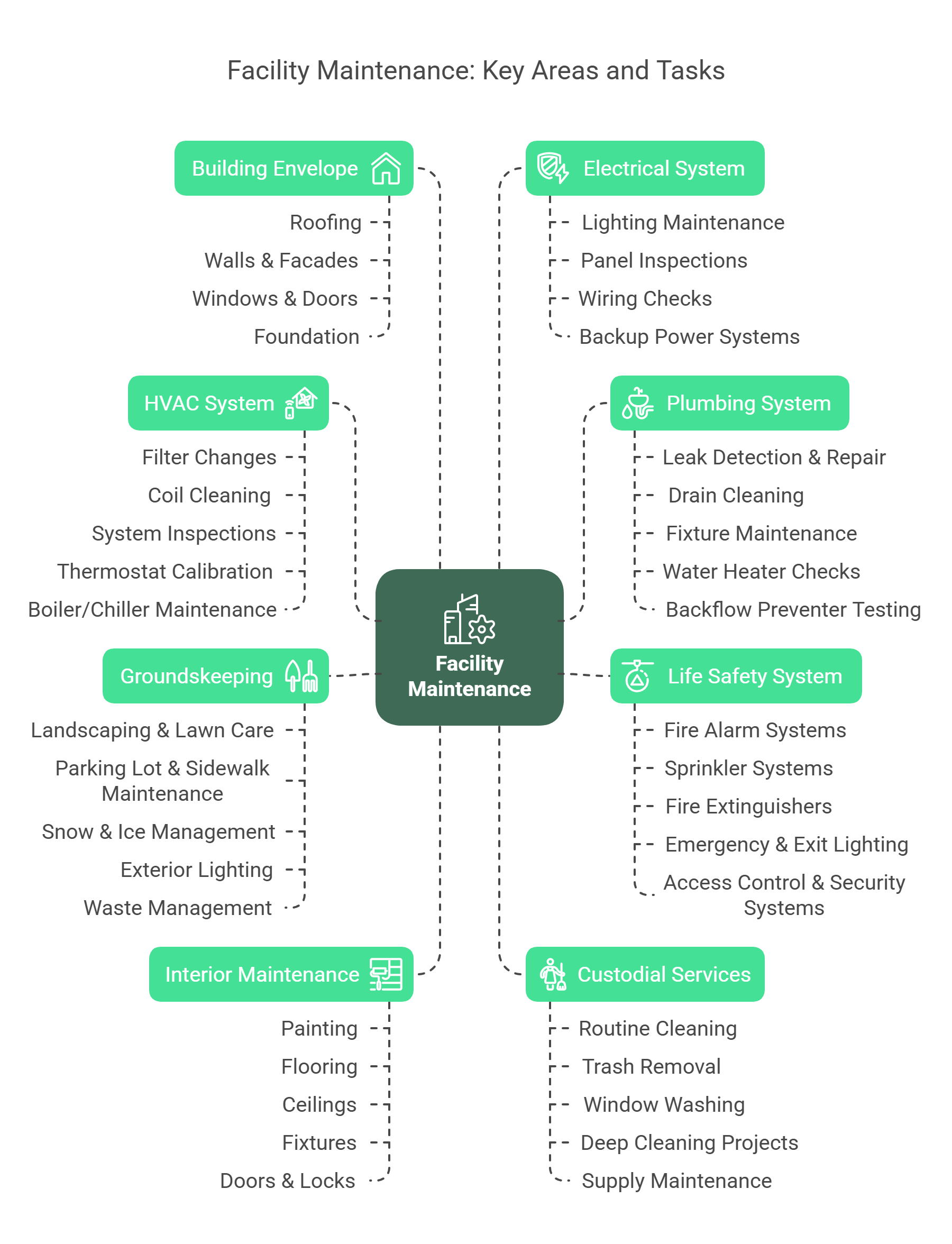
1. Building Envelope Maintenance: The First Line of Defense
The building envelope is what separates the inside from the outside – the roof, walls, windows, doors, and foundation. Maintaining its integrity is crucial for preventing water intrusion, air leaks, pest issues, and structural problems.
- Roofing: Regular inspections (at least twice a year and after major storms) to check for damaged shingles/membranes, flashing issues, clogged drains/gutters, and signs of leaks. Prompt repairs are essential to prevent costly water damage.
- Walls & Facades: Checking for cracks, water staining, damaged siding or masonry, and ensuring sealant around joints is intact. Periodic cleaning may also be necessary.
- Windows & Doors: Inspecting seals and weatherstripping for air leaks, checking hardware (hinges, closers, locks) for proper function, repairing cracks or damage.
- Foundation: Looking for cracks, settlement issues, or signs of water penetration.
2. HVAC System Maintenance: The Comfort Command Center
Heating, Ventilation, and Air Conditioning (HVAC) systems are vital for occupant comfort, health (air quality), and energy efficiency. They are often complex and require regular, skilled attention.
- Regular Filter Changes: Perhaps the single most important PM task. Dirty filters restrict airflow, reduce efficiency, worsen air quality, and strain equipment. Frequency depends on the system and environment.
- Coil Cleaning: Cleaning evaporator and condenser coils ensures efficient heat transfer.
- System Inspections: Checking refrigerant levels, belts, motors, drains, electrical connections, and overall system operation.
- Thermostat Calibration: Ensuring thermostats accurately read and control temperature.
- Boiler/Chiller Maintenance: More intensive seasonal checks and servicing for central plant equipment.
3. Electrical System Maintenance: Powering Productivity & Safety
From keeping the lights on to powering critical equipment, electrical systems are fundamental. Maintenance focuses on safety and reliability.
- Lighting Maintenance: Replacing burned-out lamps/bulbs promptly. Group relamping (replacing all lamps in an area at once) can be efficient. Cleaning fixtures improves light output. Consider energy-efficient upgrades (like switching to LEDs).
- Panel Inspections: Visually inspecting electrical panels for signs of overheating (discoloration), loose connections, or corrosion. Thermal imaging inspections can proactively detect hot spots.
- Wiring Checks: Looking for damaged insulation, loose connections, or overloaded circuits (though detailed checks often require licensed electricians).
- Backup Power Systems: Regularly testing backup generators and Uninterruptible Power Supplies (UPS) under load to ensure they function correctly during an outage.
4. Plumbing System Maintenance: Keeping Things Flowing
Plumbing issues can range from minor annoyances to major water damage disasters. Proactive maintenance focuses on prevention and efficiency.
- Leak Detection & Repair: Regularly checking pipes, fixtures (faucets, toilets), and water-using appliances for drips or leaks. Even small leaks waste significant water and can cause hidden damage over time.
- Drain Cleaning: Preventive drain cleaning, especially in high-use areas (restrooms, kitchens), helps prevent clogs and backups.
- Fixture Maintenance: Repairing running toilets, dripping faucets, or malfunctioning valves promptly. Ensuring proper water pressure.
- Water Heater Checks: Inspecting traditional tank heaters for leaks or corrosion; flushing tanks periodically to remove sediment. Checking tankless systems according to manufacturer guidelines.
- Backflow Preventer Testing: Required by regulation in many areas, these devices prevent contaminated water from flowing back into the clean water supply and need regular testing by certified plumbers.
5. Life Safety System Maintenance: Non-Negotiable Protection
These systems are critical for occupant safety during emergencies. Maintenance is often mandated by code and requires meticulous record-keeping.
- Fire Alarm Systems: Regular testing of detectors (smoke, heat), pull stations, notification appliances (horns, strobes), and control panels according to fire code requirements (often NFPA standards).
- Sprinkler Systems: Periodic inspections of sprinkler heads, valves, piping, and fire pumps. Flow tests may be required.
- Fire Extinguishers: Monthly visual inspections and annual maintenance/certification as required by code.
- Emergency & Exit Lighting: Regular testing to ensure batteries and bulbs function correctly during power outages.
- Access Control & Security Systems: Testing door locks, card readers, security cameras, and alarm systems to ensure they function as intended.
6. Groundskeeping & Exterior Maintenance: Curb Appeal and Safety
The exterior of your facility is the first thing people see, and grounds maintenance impacts both aesthetics and safety.
- Landscaping & Lawn Care: Mowing, edging, weeding, fertilization, pruning shrubs and trees (important for preventing damage to buildings or power lines).
- Parking Lot & Sidewalk Maintenance: Repairing cracks and potholes (trip hazards), sealcoating asphalt, ensuring proper drainage, re-striping parking spaces, maintaining signage.
- Snow & Ice Management: Crucial in colder climates for maintaining safe access for vehicles and pedestrians. Requires planning for plowing, shoveling, and de-icing.
- Exterior Lighting: Ensuring parking lot lights, pathway lights, and building security lights are functional.
- Waste Management: Managing dumpsters and recycling areas.
7. Interior Maintenance: Upkeep Inside the Walls
Maintaining the interior spaces keeps them functional, presentable, and pleasant for occupants.
- Painting: Touch-ups for scuffs and damage; periodic repainting of walls and trim.
- Flooring: Regular cleaning, repairing damaged tiles or carpet, refinishing wood floors, addressing trip hazards.
- Ceilings: Replacing stained or damaged ceiling tiles, ensuring structural integrity.
- Fixtures: Repairing or replacing damaged light fixtures, restroom dispensers, door hardware, etc.
- Doors & Locks: Ensuring doors close properly, locks function correctly, and hardware is secure.
8. Custodial & Janitorial Services: Cleanliness and Sanitation
While sometimes managed separately, cleaning services are deeply intertwined with facility maintenance and overall building health.
- Coordination is Key: Facility maintenance often needs to coordinate with cleaning crews for access, reporting issues (like leaks discovered during cleaning), and managing waste removal.
- Scope: Includes routine cleaning (vacuuming, mopping, dusting, restroom sanitation), trash removal, window washing, deep cleaning projects, and maintaining supplies.